Introduction
One of the stable global trends in the production of mineral fertilizers in recent years is the rise in the production and consumption of complex magnesium fertilizers. The rise in the use of high-concentration fertilizers, the rise in productivity, and hence the rise in the use of nutrients, including magnesium in the soil, make the task of compensating for magnesium losses more and more urgent. The methods of obtaining complex magnesium fertilizers during acid processing of various types of magnesium-containing raw materials are known. In this article, we studied the method of obtaining magnesium-containing mineral fertilizer with certain chemical-physical properties.
The research was conducted to prepare magnesium-containing fertilizers based on several types of local raw materials and products. Information about the rheological properties of the obtained suspensions was obtained at this time, which, in turn, made it possible to justify the optimal conditions and methods of introducing components containing magnesium, nitrogen, and potassium into the technological process.
The acquisition of mineral fertilizer by breaking down dolomite, a magnesium carbonate raw material, with sulfuric acid of different concentrations in a wide range of concentrations (30-70%) and adding a nitrogen-containing component to the obtained slurry was studied in the research.Basically, at low concentrations of acid, the decomposition of dolomite is completed in a relatively short time, and at relatively high concentrations of acid, the time required for the decomposition of dolomite is slightly extended.
In the research, 30-70%, at 60°C temperatures of 30-70% and 60°C, slurries obtained from the decomposition of dolomite were used.
The degree of decomposition of the raw material was calculated using the hora sample taken during the decomposition of dolomite with sulfuric acid.
At the time of crystallization of various solid phases, the nature of the mineral, the rate and concentration of sulfuric acid, the precipitating properties of magnesium phosphate salts, and the speed and degree of decomposition in all M: B ratios were found to have a significant effect.
The obtained results show that in all cases, the increase in the rate of decomposition as a function of time manifests itself as an important feature of the process and is known to affect the existing regularity. The physicochemical basis of the processes occurring during the purchase of magnesium-containing complex fertilizers by splitting phosphate raw materials or dolomite with acid and adding a nitrogen-containing component to the reaction was studied. Based on the literature data, it was concluded that, based on the analysis of the technological processes for the production of mineral fertilizers and equipment, it is necessary to decompose phosphate and magnesium-containing raw materials with sulfuric acid, then neutralize the resulting phosphate acid suspension, granulate it, and obtain a complex magnesium-containing fertilizer by drying the finished product more convenient.
The increase in the use of high-concentration fertilizers, the increase in productivity, and, in connection with this, the increase in the output of nutrients, including magnesium, make the problem of compensation for magnesium losses more and more urgent. Based on numerous agrochemical studies, it has been proven that magnesium-containing fertilizers have a positive effect on both the volume and quality of the crop against the background of NPK [1].
During the studies, the physicochemical properties of the application of magnesium-containing components at different stages of the production of superphosphate and complex magnesium-containing fertilizers, and the mineralogical composition and physical-mechanical properties of the products formed at separate stages of the production of complex magnesium-containing fertilizers were studied.
The analysis of the known methods of obtaining magnesium-containing fertilizers shows that the most interesting method is based on splitting phosphorite with nitric acid, and then mixing nitric acid with urea and potassium chloride. Using sulfuric and phosphoric acids, the authors studied the possibilities of applying magnesium-containing raw materials at different stages of phosphate raw material decomposition [4].
One of the most popular mineral fertilizers in the world market, 15:15:15:5, was selected as the base brand of fertilizers, and this fertilizer is considered a balanced full-complex magnesium-containing fertilizer [5].
During the research, the effect of the duration and temperature of the magnesium-containing raw materials decomposition process with acid, as well as the concentration of sulfuric acid on the decomposition process and the main technical indicators were studied.
The combined application of dolomite with phosphate raw materials has hurt both the content of different forms of P2O5 and the degree of decomposition. The decomposition of phosphate raw materials decreases, which is related to the magnesium contained in dolomite, the negative effect of which on the process of acid decomposition of phosphate ores was also noted by other authors [2, 3].
The analysis of the obtained results allows us to conclude that dolomite should be included in the suspension formed after the decomposition of the main part of phosphorite. The consumption of sulfuric acid with the combined application of primary phosphorus- and magnesium-containing raw materials was calculated based on the condition of co-degradation of phosphorite and dolomite, therefore, if only phosphorite is included, the actual amount of sulfuric acid that causes the decomposition of raw materials at the beginning of the process turns out to be more.
Let’s take a look at the value of the decomposition rate of raw materials containing magnesium and phosphorus with sulfuric acid with a concentration of 66% at a temperature of 60℃ for 90 minutes. The value of the decomposition rate during the joint decomposition of dolomite and phosphorite is equal to 84.43. During the decomposition of dolomite and then the inclusion of phosphorite, the decomposition rate is equal to 90.25. In the case of the decomposition of phosphorite and then the inclusion of dolomite, the decomposition rate is equal to 92.38. As we can see, the greatest degree of decomposition is possible in the case of inclusion of dolomite after the decomposition of phosphorite.
The results of the study of the effect of temperature on the general decomposition rate of phosphorite in the presence of dolomite are given in figure 1. The maximum decomposition rate of 96.42% is achieved at a temperature of 90єС, but decomposition at this temperature is accompanied by a significant thickening of the suspension. This fact is related to the negative effect of the formed magnesium phosphates, which is confirmed by literature data. The introduction of an additional liquid phase, which is necessary to achieve sufficient fluidity, is not desirable, because it will lead to a violation of the balance and a significant increase in energy costs in the drying phase for the next cycle [4]. Taking this into account, the optimal temperature is 80 ° C, at which the degree of decomposition reaches 91.34% and the resulting suspension maintains its fluidity.
It was determined that during the first 90 minutes, the main amount of raw material is decomposed, then when the decomposition time increases to 180 minutes and more, the suspension thickens until the fluidity is completely lost. This is explained both by the formation of calcium sulfate particles formed during the decomposition of phosphate raw materials and by the process of formation of crystals that make further processing of the resulting suspension impossible according to the existing technology. Thus, the optimal duration of the process should be 90-120 minutes.
However, even under these conditions, the maximum degree of decomposition does not exceed 90-92% when using only sulfuric acid. To obtain a specific brand of fertilizer in terms of nitrogen content, it is necessary to study together the process of adding the nitrogen-containing component by the technological balances performed.
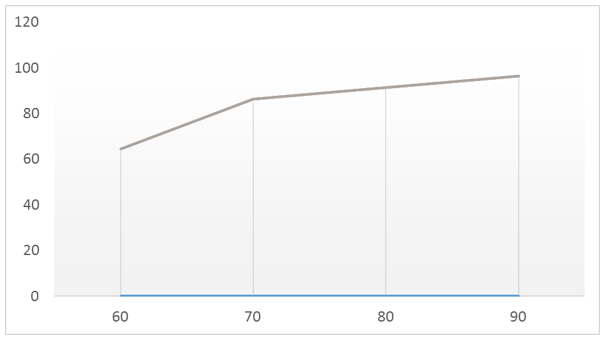
The analysis of the obtained data allows us to conclude that the decomposition coefficient increases from 5% to 7% during the joint decomposition with a mixture of acids compared to the decomposition using only sulfuric acid. is the organization of a process: keeping the concentration of sulfuric acid in the liquid phase at 55 masses %, primary decomposition of phosphate raw materials with a mixture of sulfuric and phosphoric acids, phosphorus – 22 mass %, and subsequent introduction of magnesium-containing raw materials (dolomite) into one of the last sections of the reactor. The decomposition temperature is 80°C, and the total duration of the decomposition stage is 90-120 minutes. Under these conditions, the total decomposition rate of raw materials reaches 96.42%.
Based on the conducted research, the following scheme is proposed: stepwise decomposition of phosphate and magnesium-containing raw materials with sulfuric acid, the introduction of urea – a nitrogen-containing component into the suspension (it is known that the introduction of urea as a nitrogen-containing component improves the rheological properties. Urea can be fed into the process at any stage However, it is better to introduce urea into the suspension after the decomposition stage, characterized by the lowest viscosity and maximum fluidity) [4].
Thus, two possible options are offered for the implementation of the technological process, which includes different methods and the sequence of application of reagents, namely:
1) after splitting the phosphorite concentrate with acid, first dolomite is added to the phosphate suspension, and then nitrogen-containing component-urea.
2) decomposition of dolomite with acid and all subsequent stages are carried out according to the previous option.
As previously identified by the authors, when NPK fertilizer is produced, various chemical reactions occur at separate stages of the process, including ammonium salts and potassium chloride exchange reactions, the formation of double salts (phosphates and sulfates), as well as urea co-hydrolysis and dehydration of phosphoric acid with polyphosphate formation. interactions occur [5]. The course of these reactions leads to the fact that the resulting fertilizers are a multicomponent system, and the application of magnesium compounds undoubtedly contributes to the occurrence of additional processes and the complexity of the phase composition of fertilizers.
All magnesium in the resulting fertilizer is soluble in water, when dolomite is used, water-insoluble magnesium compounds are also present, although the decomposition of dolomite with a mixture of sulfuric and phosphoric acids occurs almost comprehensively.
Since dolomite is introduced into the reaction mixture at the initial stage (after the decomposition of phosphate raw materials), the process of magnesium sulfate formation can be represented by the following reaction equation:
If the amount of sulfuric acid taken for the decomposition of dolomite is less than the above-mentioned interval amount, the degree of decomposition of raw materials will reduce. Taking more than the specified interval amount of sulfuric acid taken for dolomite decomposition cannot be considered appropriate, because it does not diminish the degree of dolomite decomposition, but instead rises the consumption of sulfuric acid.
From the conducted studies, it was determined that the size of the dolomite particles has a significant effect on the decomposition rate [6].
Processing with acids During the processing of magnesium compounds, magnesium goes into solution in the form of soluble salts. For example, during the decomposition of dolomite with sulfuric acid, almost all magnesium in the raw material goes into the liquid phase. Currently, the rate of decomposition of carbonate compounds of magnesium and calcium in raw materials is high.
The determination of the activity of H+ ions in both pure and solutions neutralized with magnesium allows us to conclude that the activity of hydrogen ions is not directly proportional to the degree of neutralization of the acid.
Conclusions
1. During the research, it was determined the possibility of obtaining phosphorus-magnesium fertilizers by replacing phosphate raw materials with dolomite to a certain extent.
2. Splitting of phosphorite and dolomite with the presence of sulfuric acid was carried out separately, and our main priority in doing this was to make better the initial cracking conditions of the raw materials taken. A new technological method was intented to propose by processing the horras which formed together during the process.
References
- Magnesium casting technology for structural applications. Journal of Magnesium and AlloysVolume 1, Issue 1, 1 March 2013.
- Vasconcelos, C., McKenzie, J.A., 2010. Dolomite as a biomineral and possible implications. Revista de la Sociedad Espaсola de Mineralogнa 9.
- Нечаева Т. В., Гопп Н.В., Савенков О. A., Смирнова Н.В. Магний в почвах и растениях в условиях склонового агроландшафта на юго-востоке Западной Сибири // Почвы и окружающая среда, 2019.
- Фирсов С.С. Эффективность магнийсодержащих удобрений на дерновоподзолистых почвах Тверской области // Агрохимический вестник, 2015.
- Аристархов А.Н. Сера в агроэкосистемах России: мониторинг и содержание в почвах и эффективность её применения // Международный сельскохозяйственный журнал, 2016.
- Байрамова А.С. Тонкая очистка природного газа от сернистых соединений // Тенденции развития науки и образования. №84, Часть 1, 2022, с. 72-75.